Optimize Your Warehouse with Used Pallet Flow Racking
Leverage our 45 years of expertise to maximize your warehouse space and streamline inventory management. National Equipment Brokers offers high-quality used pallet flow racking to enhance your warehouse efficiency, boost productivity, and ensure FIFO (First In, First Out) stock rotation.
Get a Custom Quote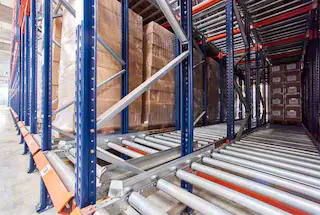
About Pallet Flow Racking
Pallet flow racking, also known as gravity flow racking, is a high-density storage system that utilizes slightly inclined lanes with rollers or wheels to allow pallets to flow from the loading end to the unloading end. This innovative design maximizes storage capacity while ensuring FIFO inventory management.
Key Features
- High-density storage (up to 100% more than selective racking)
- FIFO (First In, First Out) inventory management
- Reduced aisle space requirements
- Improved picking efficiency
- Suitable for various pallet sizes and weights
- Ideal for perishable goods and date-sensitive inventory
How Pallet Flow Racking Works
Pallet flow racking utilizes gravity and a system of rollers or wheels to move pallets through the racking system. Here's a breakdown of its operation:
Pallets are loaded from the back (higher end) of the racking system. As a pallet is placed on the lane, it automatically moves forward on the inclined rollers or wheels.
The slight incline of the lanes, combined with rollers or wheels, allows pallets to gently flow towards the picking face at the front of the system. Speed controllers ensure a safe and controlled descent.
The first pallet loaded into the system becomes the first one available for picking at the front, ensuring perfect FIFO rotation. This is ideal for perishable goods or products with expiration dates.
Forklifts remove pallets from the front of the system for order picking. As pallets are removed, the remaining stock automatically advances to the picking position. Replenishment occurs from the back, maintaining continuous stock flow.
Advantages of Pallet Flow Racking
High-Density Storage
Increases storage capacity by up to 100% compared to selective racking systems.
FIFO Inventory Control
Ensures perfect stock rotation, crucial for perishable goods and date-sensitive inventory.
Improved Space Utilization
Reduces the number of aisles required, maximizing valuable floor space.
Enhanced Productivity
Reduces forklift travel time and distances, increasing overall warehouse efficiency.
Reduced Labor Costs
Minimizes the need for constant restocking and inventory reorganization.
Increased Picking Speed
Always presents the next available pallet at the picking face for quick access.
Customizable Configurations
Can be tailored to fit specific warehouse layouts and storage requirements.
Improved Safety
Reduces forklift movement and eliminates the need for deep-reach operations.
Pallet Flow Rack Applications
Pallet flow racking is versatile and can be applied across various industries and storage scenarios. Here are some common applications:
-
Food and beverage distribution:Ideal for perishable goods requiring strict FIFO rotation, ensuring product freshness and minimizing waste.
-
Cold storage warehouses:Maximizes storage density in temperature-controlled environments, optimizing space utilization in costly refrigerated areas.
-
Manufacturing facilities:Efficient storage and retrieval of raw materials and finished goods, supporting just-in-time production processes.
-
E-commerce fulfillment centers:Supports high-volume order picking for fast-moving products, enhancing fulfillment speed and accuracy.
-
Pharmaceutical storage:Ensures proper stock rotation for date-sensitive medications and supplies, maintaining regulatory compliance.
-
Automotive parts distribution:Manages high-volume, fast-moving inventory effectively, supporting efficient supply chain operations.
-
Retail distribution centers:Enables efficient storage and distribution of goods to multiple store locations, improving inventory turnover.
-
Third-party logistics (3PL) providers:Offers flexibility for storing and managing diverse product ranges with varying turnover rates, adapting to multiple client needs.
Components of Pallet Flow Racking
- Upright frames: Vertical supports that form the structure of the racking system
- Beams: Horizontal supports that define each storage level
- Flow rails: Inclined channels equipped with rollers or wheels for pallet movement
- Entry guides: Assist in proper pallet placement during loading
- Braking systems: Control the speed of pallet descent
- Pallet separators: Ensure smooth transition between pallets
- End stops: Prevent pallets from falling off the unloading end
- Safety bars: Provide additional support and prevent pallet push-through
Visual Guide to Pallet Flow Racking Components
Understanding the key components of pallet flow racking can help you make informed decisions about your warehouse storage needs. Here's a visual breakdown of the essential elements:
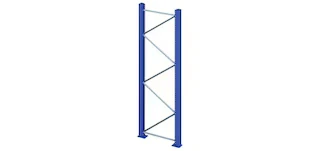
Frames: Vertical structural elements consisting of two uprights joined by cross-ties and diagonals, providing the backbone of the racking system.
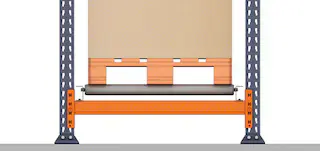
Flow Rack Beams: Horizontal supports that hold the roller tracks, allowing pallets to slide smoothly through the system.
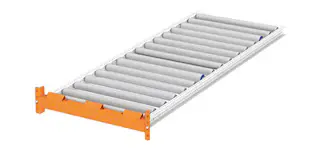
Exit Beams: Located at the end of each channel, these beams incorporate retaining stops to secure pallets at the unloading end.
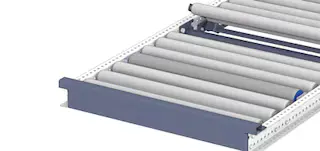
End Stops: These safety features replace the exit beam when the channel extends past the supporting beam, preventing pallets from falling.
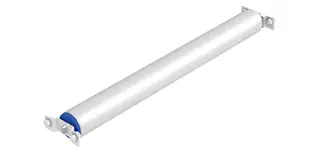
Brake Rollers: These control the speed of pallet movement, adjusting the braking force based on pallet weight and speed for safe, controlled flow.
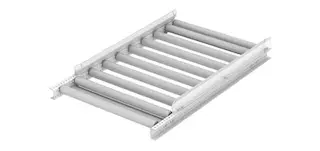
Pallet Centralisers: Positioned at the channel entrance, these guide pallets onto the correct path, ensuring smooth flow and preventing jams.
Pallet Flow Rack Manufacturers
- Interlake Mecalux
- Ridg-U-Rak
- Steel King
- Frazier Industrial
- Speedrack Products
- Unarco Material Handling
- Twinlode Automation
- Konstant
- NEDCON
- Elite Storage Solutions
- Mallard Manufacturing
- 3D Storage Systems
Each manufacturer offers unique features and specialties. Our team can help you choose the best option for your specific needs.
Choosing the Right Pallet Flow Racking
When selecting a pallet flow racking system, consider the following factors:
- Required storage depth and lane length
- Pallet dimensions, weight, and condition
- Product turnover rates and inventory characteristics
- Available warehouse space and ceiling height
- Types of forklifts used in your facility
- Specific industry requirements (e.g., food-grade, cold storage)
- Budget considerations
- Future growth projections
At National Equipment Brokers, we leverage our 45 years of experience to help you navigate these considerations and choose the perfect pallet flow racking solution for your warehouse.
Installation and Safety
Proper installation and adherence to safety guidelines are crucial for the effective and safe use of pallet flow racking. We offer professional installation services to ensure your racking is set up correctly and safely.
Safety Best Practices:
- Regular inspections of rails, rollers, and structural components
- Proper training for forklift operators on pallet flow system operation
- Use of appropriate personal protective equipment (PPE)
- Strict adherence to load capacity limits and pallet specifications
- Implementation of a robust warehouse management system
- Clear labeling of lane contents and weight restrictions
- Immediate repair or replacement of damaged components
- Ensure proper pallet quality to prevent jams or flow disruptions
Frequently Asked Questions
What is the maximum lane depth for pallet flow racking?
Pallet flow rack lanes can typically accommodate up to 20 pallets deep, but the most common configurations range from 4 to 12 pallets deep. The ideal depth depends on your specific inventory management needs, product turnover rates, and warehouse layout.
Can pallet flow racking handle different pallet sizes and weights?
Yes, pallet flow racking can be designed to accommodate various pallet sizes and weights. However, it's important to note that each lane is typically configured for a specific pallet size and weight range. We can help you design a system that best fits your inventory needs, including mixed-use configurations if necessary.
How does pallet flow racking compare to push-back racking?
While both systems offer high-density storage, pallet flow racking operates on a FIFO (First In, First Out) basis, making it ideal for perishable or date-sensitive goods. Push-back racking, on the other hand, operates on a LIFO (Last In, First Out) basis. Pallet flow is generally deeper and better suited for higher volume, faster-moving products.
Is used pallet flow racking as reliable as new equipment?
When sourced from reputable suppliers like National Equipment Brokers, used pallet flow racking can be just as reliable as new equipment. We ensure all equipment meets quality and safety standards. Critical components like rollers and braking systems are often replaced to ensure optimal performance.
Why Choose National Equipment Brokers for Used Pallet Flow Racking
- 45 years of industry experience
- Customization capabilities to meet your specific needs
- Comprehensive service including selection, installation, and delivery
- Competitive pricing on high-quality used equipment
- Expert customer support and service
- Nationwide delivery and installation